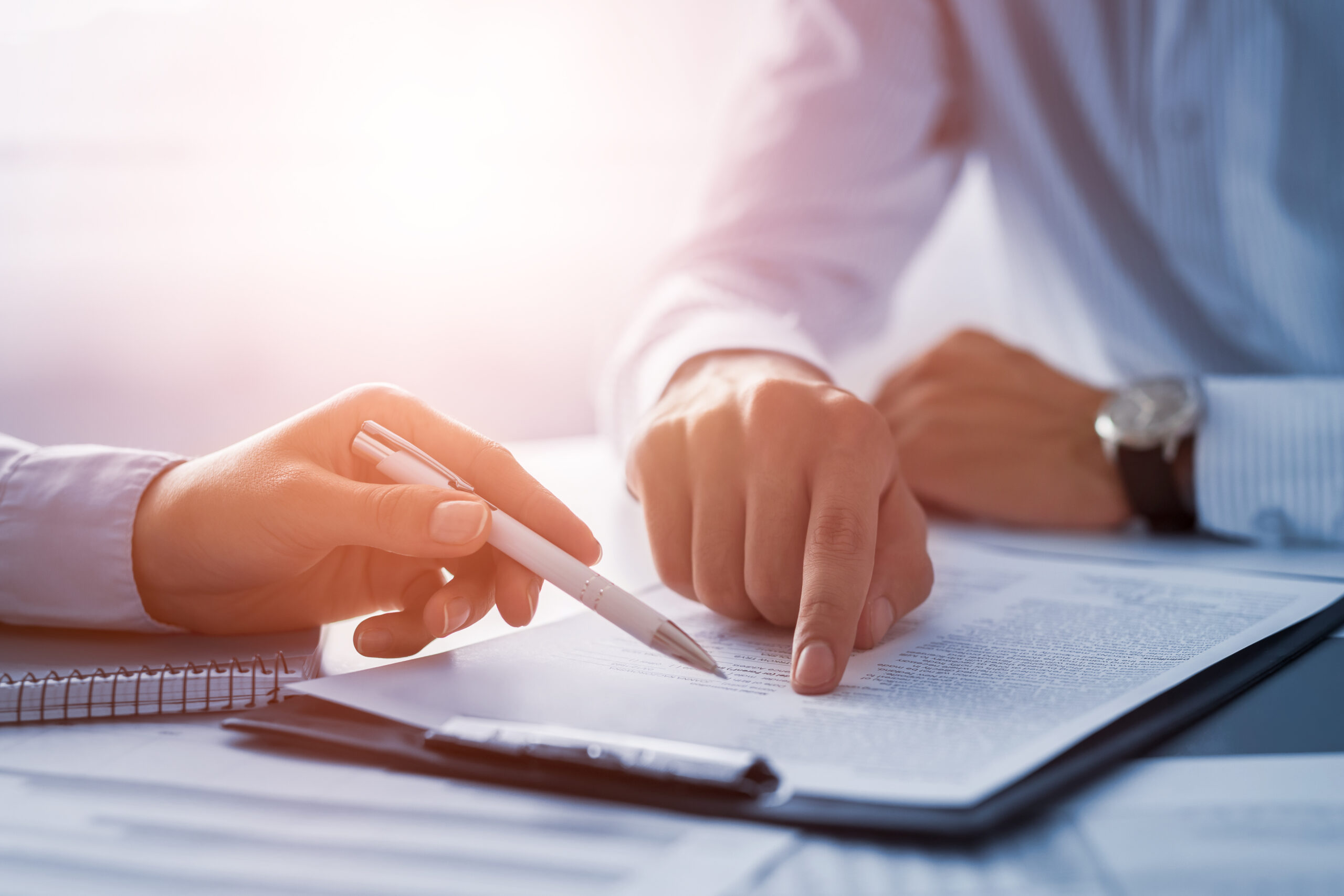
US elevators make 18 billion passenger trips every year. To put this into perspective, if 99.9999% of elevator journeys were made successfully there would still be 18,000 journeys that would experience some form of issue. It is for this precise reason that a code of safety for elevators is of paramount importance; the ASME 17.1 code is intended to provide safety of life and limb and to promote public welfare.
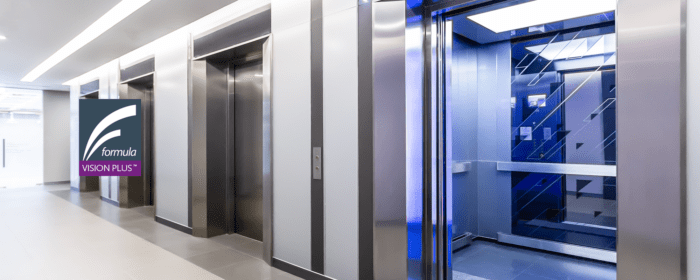
INTRODUCTION OF ASME A17.1-2022/CSA B44:22 SECTION 2.13.5
In 2019, after many years of work and significant revisions, ASME A17.1-2019 was released, and was
further revised in 2022.
The change with respect to door protection devices on passenger elevators is intended to reduce the risk
of door impact incidents by incorporating a means to detect objects approaching the elevator doors. The
code requirements are comprehensive and specific (see ‘ASME Code Compliancy’ datasheet for details).
Formula Systems used the Voice of the Customer (VoC) to inform the design process, resulting in a
patented, market disruptive solution; the Vision Plus elevator door safety edge solution.
VISION PLUS UTILIZES ADVANCED TECHNOLOGY TO STAND OUT AS A MARKET LEADER IN DOOR SAFETY
One of the stand-out features of the Vision Plus is its unique approach to installation, eliminating the need for additional overhead-mounted detection units. By integrating all technology into the edges, Vision Plus reduces installation complexity, s aving valuable time and resources.
OPTIMIZED TECHNOLOGY FOR EASE OF INSTALLATION
The Formula Systems Research & Development team were briefed to investigate appropriate
technologies to ensure conformance and adherence to the new A17.1 requirements. After
two years of research, prototyping and extensive testing the result was the Vision Plus light curtain,
an ASME 17.1-2022 code compliant, third-party certified solution.
The Vision Plus solution requires no additional overhead modules, it does not require post fitting
calibration or elevator permits. It requires the same installation process as for 2D edges and as such can deliver substantial cost savings versus alternative products.
FORMULA SYSTEMS DESIGN PROCESS
The design process is informed by the VoC. Whilst gathering the VoC data the Formula Systems engineers
evaluated several potential technology solutions that were considered capable of satisfying the code
requirements.
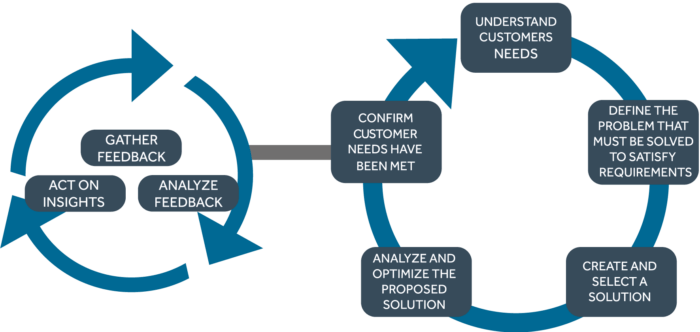
TECHNOLOGY CALIBRATION
Formula Systems evaluated the following technologies:
Time of flight: a technology that illuminates the area with a modulated light source, usually solid-state laser or near infrared LED, and observes the reflected light. The phase shift between transmitted and reflected light is measured and analyzed to determine distance.
Microwave radar: a technology that emits high frequency radio waves (microwaves) and calculates distance and position based on the reflected radio waves (similar to radar).
3D Camera: This technology uses active time-of-flight and a 3D camera to collect data and determine size and distance of objects.
Retroreflective infrared: This technology uses infrared LEDs and photodiodes in the same location (respond to a signal increase due to reflection).
Hybrid solution: Using a combination of technologies.
UTILZING THE VOICE OF THE CUSTOMER
Product attributes and features have limited value if they do not meet the customers’ needs and so the VoC data was analyzed to ensure that the needs of the customer (qualitative data used to define the development project scope) were addressed and utilized to develop customer requirements (specific measurable product characteristics and features). With the requirements clearly stated then design can be viewed simply as a series of problems to be solved.
Product attributes and features have limited value if they do not meet the customer’s needs.
The data provided, from many sources, highlighted several common themes, some examples include-
- Cost
- Simple to install
- Code compliant
- Certified product
- Shallow learning curve
- Limited or no calibration
Using the requirements developed from the VoC data, the potential solutions were weighted and scored against the full list of requirements.
The results were clear, to achieve the customers’ highest ranked requirements, the retroreflective infrared technology had the highest chance of success. Many iterations were designed, and many prototypes constructed resulting in Vision Plus.
The Vision Plus satisfies the key areas of high importance to customers and it does this because the patented design incorporates both 3D and 2D detection systems into the existing edge profiles. Using this approach, obviates the requirement to install and wire in an additional module in the elevator door header saving both time, labor and permit costs. The Vision Plus requires no calibration and fitting the curtain of light is no different than replacing a 2D edge. This also means that product training for Vision Plus does not need to be extensive. In 2022 the Vision Plus was certified by the Liftinstituut (an ANAB/ANSI accredited body) to ASME A17.1-2022/CSA B44:22 section 2.13.5
The VoC is the most important part of any product development, without this information design initiatives, we are effectively blindfolded. Products could have multiple ‘nice to have features’, and yet, not satisfy the fundamental design characteristics required by the customer.
By utilizing the VoC, Formula Systems were able to develop a product that was not only cost effective, compliant, and third party certified, but also a product that precisely satisfies the customer’s needs.
Learn more about the Vision Plus safety edge here. Our team will be happy to help if you need any further information.
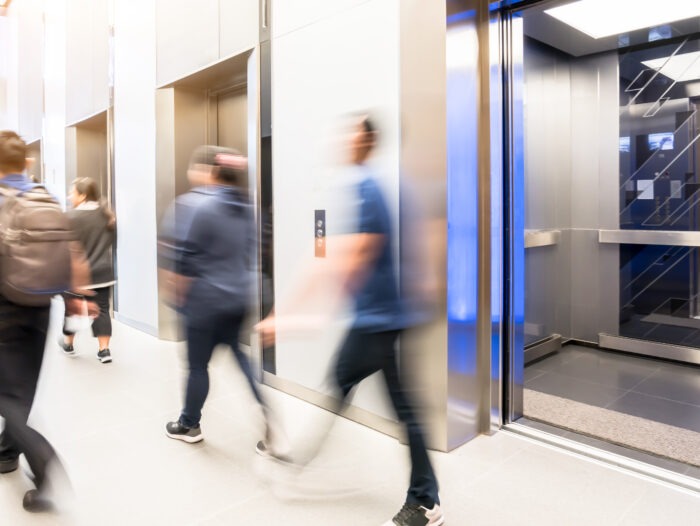